Platform Technology for Smart Augmented Reality Eyewear
ARfusion® technology combines precision cast lens fabrication tools with functional metamaterials and volume holograms, to provide AR wearable developers with a platform for seamlessly integrating smart technologies into thin lightweight prescription glasses.
Goals for Smart AR Glasses
To achieve widespread commercial adoption and ultimately become as ubiquitous as smartphones, AR glasses must be comfortable, affordable, natural looking, and easy to use. A successful solution needs to achieve high-quality images and a large field of view (FOV) in a fashionable, compact form factor, without adding excess weight. This means that the smart technologies (displays, filters, active dimming) must be embedded within a rugged, cast prescription lens.
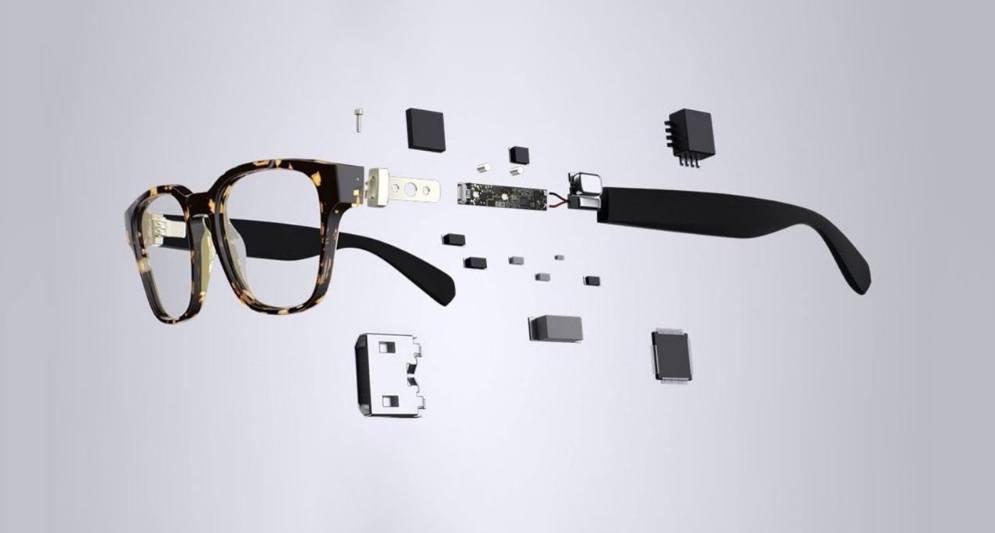
User Experience | Film Configuration |
---|---|
Full immersion | Wide field of view, image quality |
Wearability 24/7 | Low power consumption, light weight |
Ruggedness | Drop performance, scratch resistance |
Street price | Bill of materials, manufacturing cost / yield |
In the beginning, a greener approach to corrective lenses
The ARfusion® system was first developed by a Swiss company, Interglass Technology, which designed the automated lens casting system as a more sustainable solution to producing prescription lenses, using a fraction of the material and energy compared to conventional processes. The lenses were directly cast into the final correction using an extensive library of reusable front and back molds. Acrylic monomer injected between the two molds is cured with UV light in seconds. The molds are automatically separated, and the lens substrate is ready in as quick as 1 minute, with no cleaning, polishing or post-production for a simple corrective lens. To accommodate precisely formed and embedded smart AR elements in prescription lenses, ARfusion® produces an optimized, minimal thickness, semi-finished blank lens, ready to be ground to the final curvature on standard ophthalmic processing equipment.
ARfusion® Lens Casting
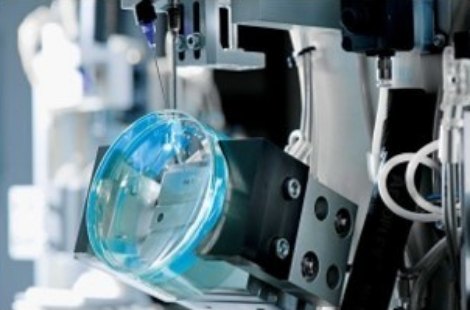
- Monomer injection between two molds.
- Automatic mold selection.
- Curing under UV light within seconds.
- Temperature <100°C, safe for holographic films or other sensitive elements.
- Automatic separation of the mold-lens-mold package.
- ~1 minute from liquid monomer to finished lens.
- Surfacing and finishing using standard ophthalmic equipment.
VS
Traditional Freeform Surfacing
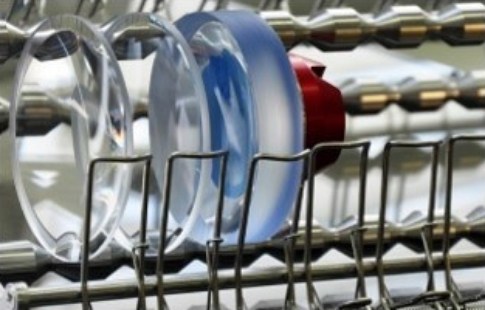
- Casting of the lens blank.
- Thermal curing for up to 50 hours in oven.
- Temperature >150°C, not suitable for holographic films.
- Blocking of the blank.
- Grinding the prescription into the blank.
- Polishing.
- Manual cleaning.
- De-blocking of the lens.
- Quality control.
In a traditional cast plastic lens, up to 80% of the original lens blank material is wasted as the prescription is ground into the blank. With the same amount of material, ARfusion® can produce several optimized semi-finished lenses. In a standard thermal process, curing of semi-finished lens blanks for up to 50 hours requires much more energy and process time compared to the UV curable materials and associated processes used by ARfusion®.
ARfusion® is Compatible with a Wide Range of Embedded Smart Technologies
The ARfusion® process uses low strain thermoforming of functionalized films (such as holographic optical elements). The foils or other components are precisely aligned within the mold cavity. The low temperature (< 100° C) does not damage sensitive films. There is high adhesion of film materials, and components are protected with the final cast lens.
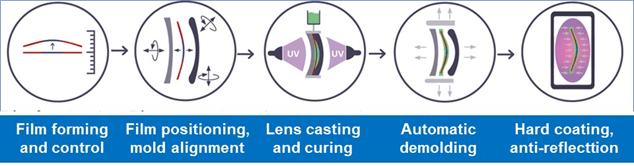
A variety of devices may be embedded within the cast lens, including waveguide and micro-displays, liquid crystal and electrochromic foils, micro-cameras and LEDs, polarized foils, sensor foils, holograms, flex circuits and antennas.
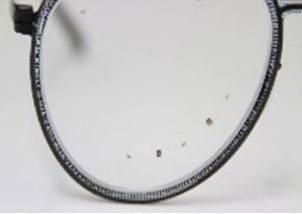
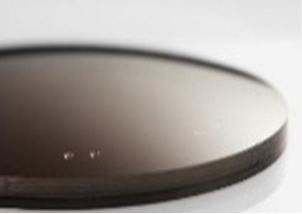
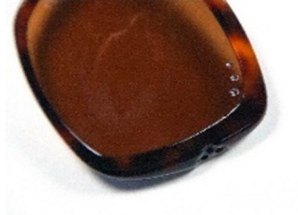
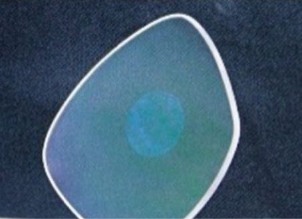
META Holographic Optics Advantages
META’s holographic components are based on photosensitive polymers, are custom-designed and are suitable for product integration by lamination, thermoforming, plastic injection molding and casting. All holographic functions can be realized in a film form factor that can be invisibly integrated into what appears to be a normal eyewear lens, and in other applications where high transparency is required.
Advantages of holoOPTIX® holographic optical components
- High diffraction efficiency (resulting from Bragg grating)
- Large areas and customizable shapes
- Flexible (plastic) substrates
- Stackable thin layer (<100 micron) solutions
- High transparency outside design (angle/wavelength) band
- Low material absorption
- Prescription set by grating pitch and slant angle. No need for material change additional layers, etc.
- Reflection and transmission configurations
- Complex and multiple optical functions
- Lightweight
- Low cost roll-to-roll manufacturing
A Suite of Materials, IP, and Proprietary Equipment
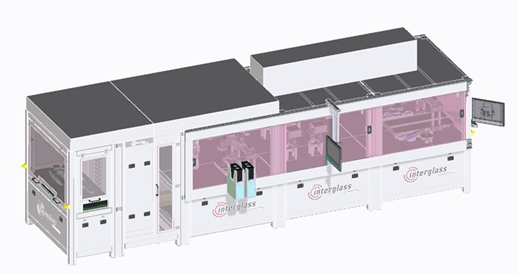
META has a multi-year supply deal with Covestro Deutschland AG, which provides early access to new photo-sensitive holographic film materials, the building block of META’s holographic product. This agreement not only allows unprecedented early access to Covestro’s R&D library of photopolymer films but will help accelerate META’s product development and speed of innovation. META acquired from North, Inc. the 1st and 2nd generation roll-to-roll holographic manufacturing technology originally developed by Intel for their Vaunt AR glasses.
META acquired the assets and IP of Interglass, including second-generation, ALC5 lens casting equipment and related workstations and software, tools, and test equipment, along with intellectual property including patents, trademarks, know-how, technical data, proprietary software, designs, and trade secrets. Interglass had 35 international patents in the field of casting processes for high-quality plastic lenses or other optical components based on UV curing acrylics. META also acquired a first-generation, Interglass ALC 4 system, formerly owned by North Inc., in Kitchener, Ontario.

META is Ready to Bring Your AR Vision to Life
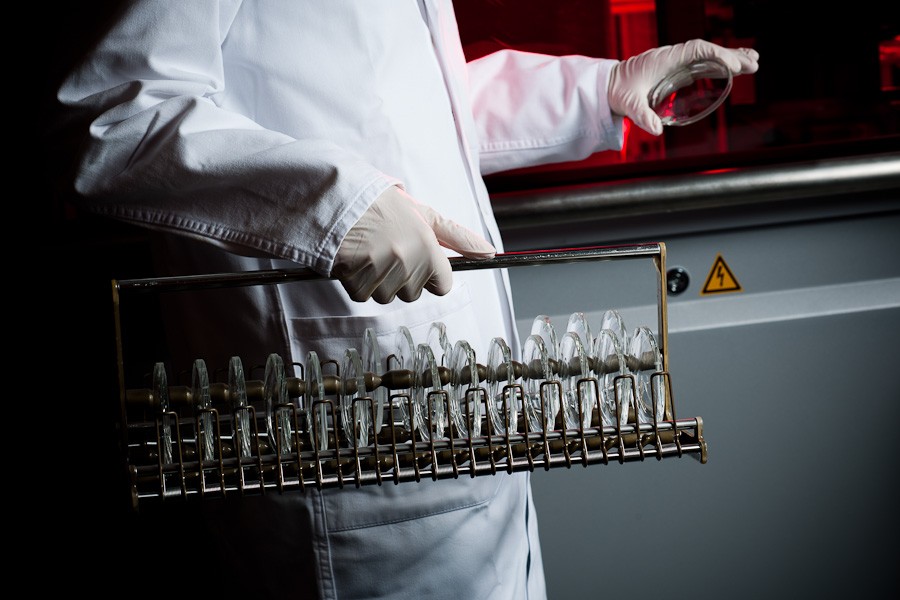
META stands ready to help AR platform developers meet the challenges of fashionable, functional AR smart glasses. The ARfusion® platform brings together the two critical elements of embedded smart technology within a lightweight and prescription capable cast lens. Delivering on the vision of augmented reality is a complex engineering task. META brings together a vertical solution encompassing materials, holographic and optics expertise, specialized equipment, and IP.